The block solution that produces and labels PET bottles
Impressive efficiency!
Blocking a stretch blow moulder and labeller brings many advantages. And that is the reason why we have further perfected the combination of both machines in one block. With a seamless drive concept, finely tuned transfer interfaces for every production program and precisely operating processes in stop situations, you can count on getting the very best out of your PET bottle production.
At a glance
- Functions: Stretch blow moulding and labelling
- Output: Up to 100,000 containers per hour*/**
- Processing range:
- Cylindrical and square PET containers
- Container volume up to 3.5 litres
- Standard and lightweight containers
- Containers of up to 100 percent rPET
- Self-adhesive labels and reel-fed plastic labels
*Depending on the processing range | **With use of Krones air conveyor system limited to max. 72,000 containers per hour
Functions and structure
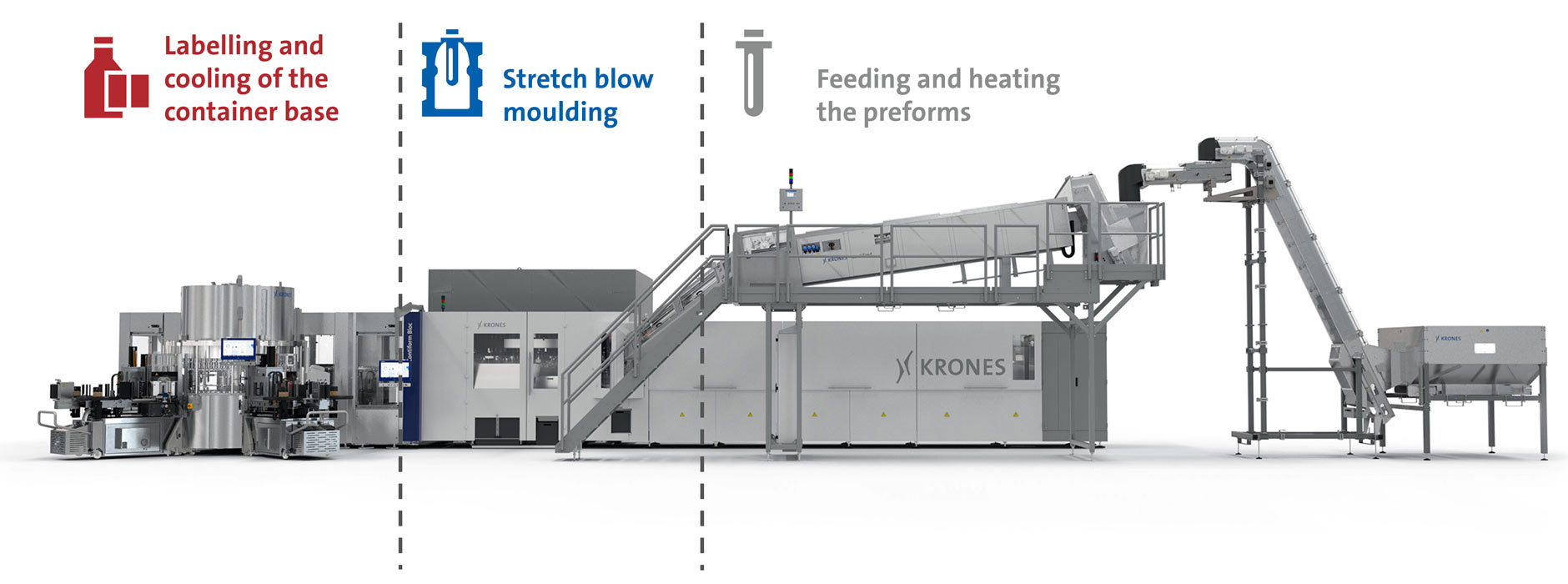
Components
- Torsion-resistant platform with skip-and-run technology
- Only four internal horizontal preform and container transfer points
- Actively controlled transfer grippers
- Five high-precision Monotec servo motors with real-time synchronisation
Infrared heating technology
- Parabolic reflector for top infrared emitter
- Adjustable base reflectors: adjustable to the respective preform length
- Maintenance-free system of ceramic reflectors
Air Wizard Triple
- Further developed compressed air recycling system with intermediate pressure levels for internal re-use of the compressed air
- Automatic self-optimisation of the blowing air recycling process
- Significantly reduced switching time dispersion
Why label first and fill afterwards?
- Full bottles can have varying internal pressures.
- These variations can impact the labelling result.
- The bottles do not have any unwanted moisture.
Solution: Contiform Bloc BL…
- labels the bottles before filling them.
- pressurises the empty bottles with compressed air.
Result
- Consistently excellent label fit
- Optimum conditions for lightweighting
- Ideal access for handling parts change-overs
- Optimal accessibility from three sides
- "No bottle – no label" function
- Reduced hotmelt consumption due to "Gravure Glue Application"
- Unique servo motor technology
- Flexible selection of the pitch
- Maximum stable handling of thin, sustainable films
Drive technology
Servo drives use throughout all applications
- Energy-efficient
- Low wear
- Reliable
Transfer technology
- Actively controlled transfer grippers
- Actively controlled transfer grippers
- Quick and very precise preform and bottle transfer
- Smallest possible contact area between the material and the machine
- Gentle conveyance also for light-weight containers
- Reduction of handling parts
- No PET abrasion during the transfer
Servo Joint Control (SJC)
Single machines or block mode? Both is possible: Because with the Servo Joint Control, you can electronically decouple the blow moulder, labeller and filler from the block.
- Automatic decoupling during malfunction
- Automatic synchronisation during restart
- Manual decoupling of individual machines for efficient change-over processes
SJC makes it possible: The Contiform Bloc BL thinks on its own!
Bottle design and moulds
Creative and in line with the market
At a glance
- Four production centres worldwide with state-of-the-art manufacturing technology
- Container design experts at all four locations
- Design and production of mould types for all Contiform series
- Mould validation on our own technical centre systems
Benefits to you
- Customer-oriented consulting: Creative, functional, unique
- Individual designs with a view to customer requirements and feasibility in the beverage line
- Experience from more than 20,000 moulds per year
Benefits to you
One operator for all machines
The block is designed as one unit in which all essential control and function elements are centrally combined. This way, just one operator can easily operate the entire Contiform Bloc BL on his own.
Trouble-free continuous operation
Full power with no breaks: The labelling module automatically detects bottle gaps and does not apply glue or labels in this case. Disruptions due to missing bottles and unnecessary glue and label consumption are therefore not an issue.
Cost-efficient customisation
The pre-defined option packages enable to adapt the block to special requirements and keep the costs as well as the commissioning time low at the same time.
Gentle treatment for PET containers
The active transfer grippers only touch the preforms and bottles in their neck area. This makes the contact area between the material and the machines as small as possible and minimises the risk of damage.
Energy savings
From the servo drives to the electromagnetic and compressed-air free stretching systems: The topic energy efficiency goes all the way through the block just like a red thread. Particularly ambitious savings targets can also be achieved with the air recycling system, which is part of the energy-saving package.
This is why the Contiform Bloc BL is enviro-classified
Energy efficiency
- Increased station performance during stretch blow moulding and labelling
- Reduced energy consumption thanks to the omission of transfer starwheels and redundant components
- Height-adjustable base thermal shield and frequency-controlled neck finish cooling system
- Energy-efficient separated vacuum during labelling
Media efficiency
- Efficient cooling of the entire block
- Air Wizard Triple air recovery system
- No compressed-air consumption during the filling process
Environmental compatibility
- Use of enviro-compliant lubricants
- Recoverable CIP media
This product is enviro classified
Top technology for ecologically efficient production
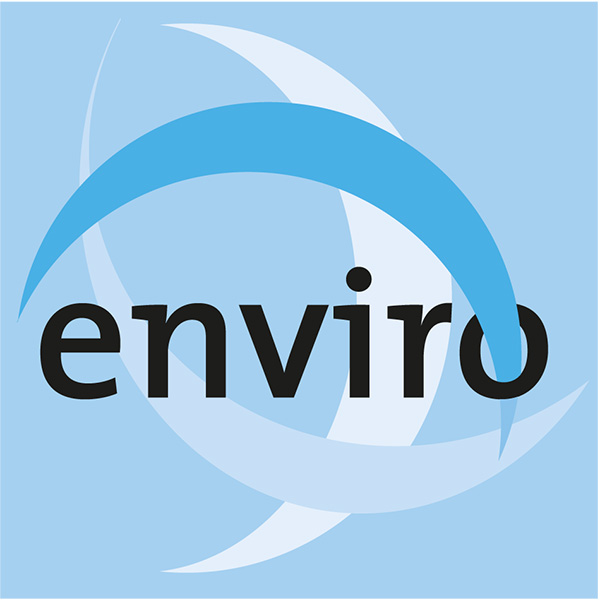
The Krones sustainability programme enviro: top technology for ecologically efficient production.